Miniature Tunnel Bore
In September of 2020, we set out to fulfill a student contract issued by the CU Hyperloop competitive team for the construction of a small digging device capable of hollowing out a 6-inch diameter structurally sound tunnel through loose packing of dirt. Below we have laid out a walkthrough of our final tunnel bore design and qualitative analysis into the decisions that we made and the effectiveness of our design methods.
The Bore
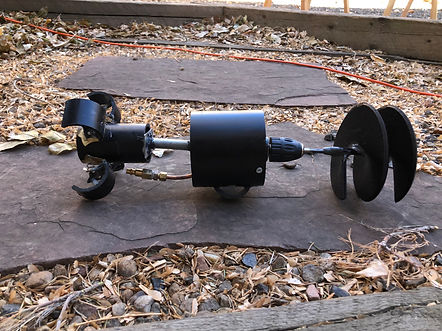



Our tunnel bore was constructed by modifying a store bought pneumatic drill, and using store bought materials modified to create our critical components. The drill operates by adding pressurized air into a rotor chamber, where several rotor blades use the air to spin the rotor, and then rotate several gears connected to the drill chuck. The drill is then encased in a piece of 4" schedule 40 ABS tubing.
The movement system operates by building up pressure between a 3/8" piece of copper tubing and a 1/4" piece of copper tubing. the resulting pressure allows the two to expand until two holes are revealed to dump pressure allowing a spring to contract the system again. This system is stabilized by the fins on the back component. allowing backwards pressure against the tunnel of the wall to help with forward propulsion.
The final component of our tunnel bore is the dirt auger. This auger is 6" in diameter and 3D printed using the material PETG. Our final design for our auger was decided on based off of two other failed augers printed in the same material. The final auger design includes fillets on all stress points, and a larger diameter shaft to reduce any stress that the drill chuck might exert on the auger.


Design CAD and Dimensioning
Auger


Bottom Component Hinge

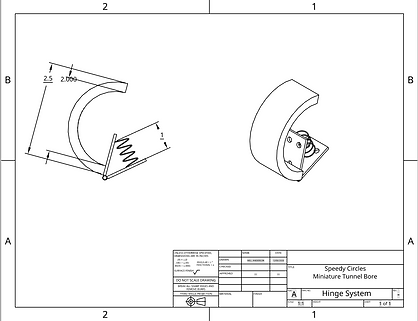
Full Body Design
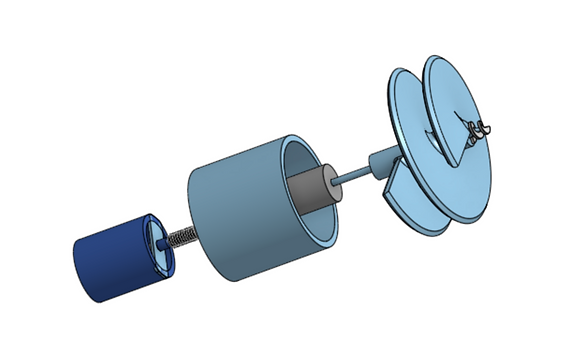
